(2) SUBSTRATE COLONISATION
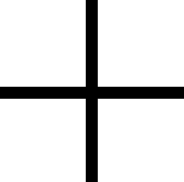
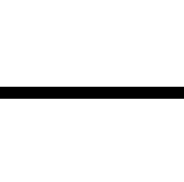
(2) Shaping and mycelium growth
Our material is produced by adding the selected fungi to an organic substrate (e.g. sawdust or textile waste). When combined - a process called inoculation - the fungi obtains nutrients from the substrate to grow its mycelium.